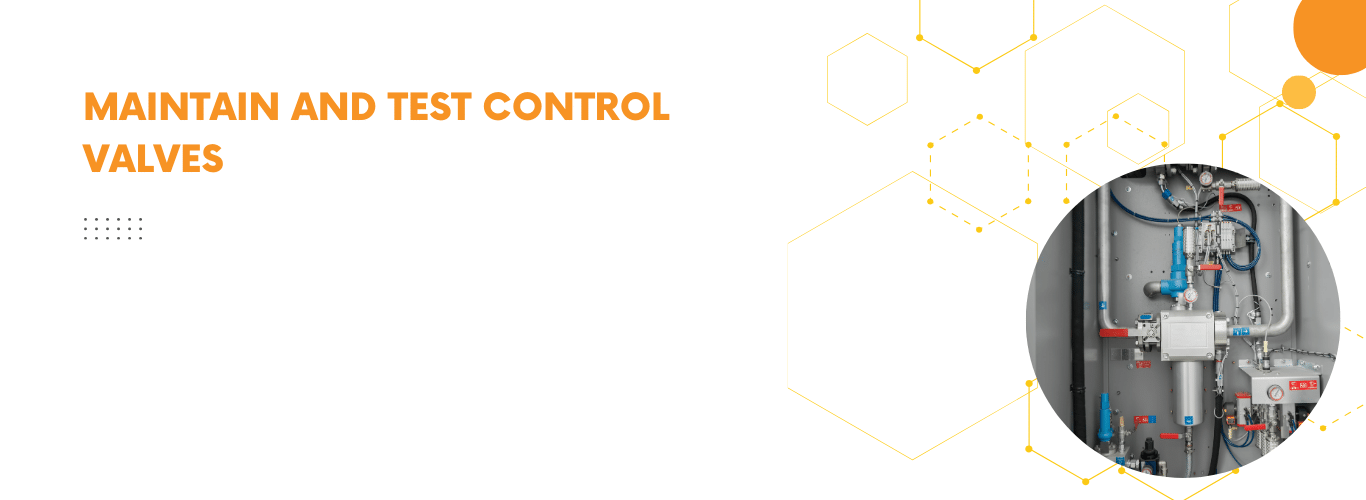
Course Objectives:
Upon successful completion of this course the participant should be able to understand:
- Purpose of a control valve and how it works to regulate flow or pressure (process parameters)
- What happens inside the control valve?
- Examples of process applications of control valves
- General performance requirements of control
- Recognize a classification of control valve ty
- Recognize the setting up and testing tasks for
- Control valve function tests type and procedure.
- Know the key features of each type of control valve and how these may help to solve problems.
- Understand the tasks involved in valve maintenance
- Understanding Control valve maintenance strategies
- Develop your knowledge of important installation features relevant to good maintenance
- Recognize the setting up and testing tasks for
- Principles of actuators for control valves
- Pneumatic actuator types
- Electrical actuators
- Hydraulic actuators for large valves
- The purpose of a positioner
- Understand the causes of control valve noise and ways to reduce
- Know the principles of a noise prediction calculation
- Recognize issues of corrosion and wear
- Consider seating materials for tight shut off versus durability
- Be aware of the problem of leaks from seals
- Know about the application of bellows seals for toxic m
- Understanding cavitation phenomenon and problem
Training Methodology:
- Participants will learn by active participation during the program using exercises, questionnaire, syndicate and group discussion
Who should attend:
Engineering and maintenance staff in oil and gas field
Course Outlines:
1. Introduction to Control Valves and Fluid Flow
1.1 Purpose of a control valve
1.2 Choked Flow Conditions (Critical Flow)
1.3 Typical control valve applications
1.4 Requirements of control valves
2. Types of Control Valves
2.1 Broad classification of control valves
2.2 Sliding stem valves.
- Globe valve.
- Globe valve construction.
- Single port double port stem.
- Cage guided valve.
- Balanced & unbalanced plug.
- Gate valve construction.
- Diaphragm valve construction.
2.3 Rotary Valves.
- Butterfly valve construction.
- Ball valve types and construction.
2.4 Other types of control valves.
2.5 Siding stem packing types & material
3. Control valve Actuators & positioners
- Function of actuators.
- The Different types of actuators.
- Advantages & Disadvantages
- Selection of actuators & parameters to be consider
- Sizing of actuators & parameters to consider.
- Performance Tests on Actuators
- Force / Torque Demanded by valves
- Actuator types – operation.
- The purpose of positioners
- How positioners linearize installed characteristics.
- Smart
4. Control valves function testing
- Test procedure to verify valve traveling.
- Details of test procedures.
- What are some of the things that are checked?
- Setting limit switches on valve.
- Hydrostatic testing.
- Why valve Hydrostatic test is performed?
- ANSI standard for pressure test.
- ANSI standard for duration of the test.
- Valve seat leakage testing.
- Why valve seat leakage is performed?
- ANSI specifications class regarding seat leakage test.
- Control valve seat leakage classifications.
- Class VI max. Seat leakage allowable.
- Reasons for valve failed in seat leakage test.
- Capacity test.
- Fugitive Emissions.
5. Key issues for Control Valve maintenance
5.1 Scope of Maintenance Activities.
- Installation practices.
- Documentation and identification of the control valve
- Filing and record keeping.
- Cost of maintenance
- Control valve maintenance strategies
- Reactive.
- Preventative
- Predictive
- Troubleshooting and diagnostics.
- Setting up of control valves and positioners
- Servicing and replacement of valve parts.
5.2 Key maintenance tasks.
- Identify and test a new control
- Stripping the valve for inspection
- Inspections and replacement of seals and stem pack
- Replacement of seat
- Changing plug and seat trim
- Servicing of the actuator and
- Setting up the valve for stroking and calibration
5.3 Isolation Standards for valve maintenance
- Single Block
- Double Block and Bleed
- Rated Spade or Spectacle Blind
- Disconnection or Line Removal
6. Major problems facing in control valve & troubleshooting
Cavitation and Flashing in Control Valves
Cavitation phenomenon and problems:
- Flashing off.
- Methods of reducing cavitation.
- Selection guide for cavitation app
- Disc Stack
Noise and Noise Reduction Methods
- Sources of control valve noise.
- Cases studies.