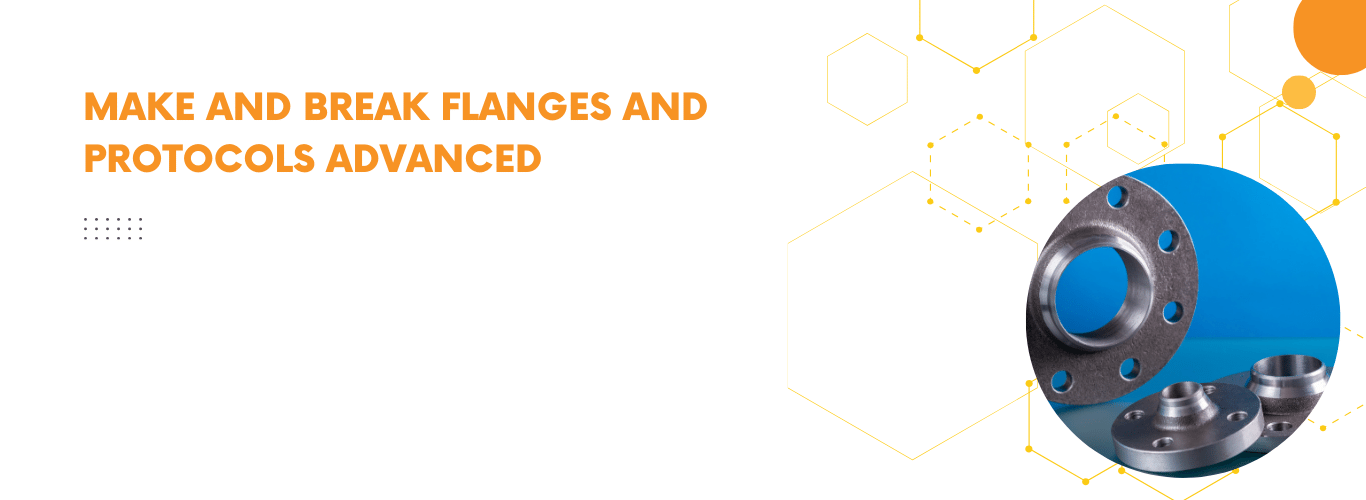
Course Overview
Flanges are very important parts of piping system in oil, gas and process industries. They provide flexibility to break the continuously running very long pipe lengths to insert fittings such as valves of various types (isolation, control, non-return, safety etc), instruments (flow, analyzers etc.), spectacle blinds, etc. Pipe flanges also allow convenient routing of pipes. Flanges are welded at both the ends of a pipe length, a valve and other fittings.
What is flange management?
Flanges help divide the whole length of pipes in smaller parts which facilitate their removals for easy inspection and maintenance. This includes their replacements for the reasons of corrosion or other types of failures/deterioration. While flanges facilitate the above aspects, they also become pain points as they are potential leak sources in high-risk process industry, e.g. oil, gas and Petro-chemicals etc which contain flammable, explosive and toxic fluids. So, the flanges of the mating pipes and fittings must perfectly match each other at the joints. This will arrest the leakage from their joints.
Why is flange management important?
Since leakage of fluids in large process industries has huge national and global economic implications, this course on ‘Flange Management and Tightening’ is very important. Only trained personnel must be asked to interface ‘Flange Management and Tightening’.
Course Objectives
This comprehensive course will equip the participants to:
- Understand features of a flange and types of flanges
- Appreciate the advantages and disadvantages of flanges in oil, gas and petroleum industry.
- Learn about types of gaskets used between flanges for sealing
- Appreciate the importance of bolts and nuts and materials of construction
- Understand concepts around torque and optimum torque, as applied to flange tightening
- The reasons for using line specifications and design standards (prior to make and break flange and where to find these).
- The impact of incorrect fitting of pipe and flanges and the main reasons for incorrect fitting.
- Demonstrate flange inspection requirements.
- Demonstrate why safe isolation of plant and equipment techniques is important.
- Coach others on applying and implementing elements of KOC Make and Break Flanges and Protocols procedures and standards.
- Explain what is required to make and break flange connections correctly.
- Explain the purpose of the design and engineering practices with respect to the choice of bolts and gaskets etc.
- Demonstrate the implications and requirements of the permit to work system.
- Assess the technical competence of others in implementing KOC Make and Break Flanges and Protocols procedures and standards.
- Management around flange tightening
- Comprehend flange bolt-tightening procedure
- Study various serious incidents due to leaking flanges in gas and petroleum industry.
- Understand care of flanges and gaskets.
- Learn about some special tools and equipment used in flange tightening
Who should attend:
- Mechanical Technicians
- Technical Authorities
- Turnaround Managers
- Commissioning Engineers
- Lead Engineers
- Reliability Engineers
- Shutdown Coordinators
- All technical pipelines and facilities personnel
Training Methodology
- Lectures (Tutor-assisted online and classroom as per prevailing situations/requirements)
- Seminars & Presentations
- Group Discussions and workshops
- Assignments
- Case Studies & Functional Exercises
Course Outlines:
Important introduction on Flow lines SPEC. & standard prior to make & break flanges.
Pipe & Pipelines specifications, codes and standards
Difference between piping and piping lines
Basic of pipe line system
Piping system component.
Definitions, terminology and Essential vocabulary
Design codes and standard.
- ASME B31.3 PROCESS PIPING.
- ASME B31.5 REFRIGERATION PIPING & HEAT TRANSFER.
- ASME B31.3 GAS TRANSMISSION & DISTRIBUTION PIPING SYSTEM.
P&ID drawing specifications
- What is a PID used for?
- How to read PID drawing.
- Details included in PID
The Types of piping Flanges (Applications, Advantages & Disadvantages).
1- standard types of flanges based on pipe attachment
- Welding Neck, Long Welding, Slip On, Threaded, Socket Weld, Lap Joint, Blind Flange.
2- special types of flanges based on pipe attachment
- Nipo, Weldoflange, Elbo flange, Swivel, Expanding Flange, Reducing Flange
3-other flange classifications
- Based On Facing, Pressure-Temperature Rating, Face Finish, Material Of Construction
4-designs, and other flange standards and markings.
- American Society of Mechanical Engineers (ASME) – ASME B16.5 & B16.47.
- ASME B16.5 Flange rating chart. API Flanges, API 6A.
Criteria of Elements and Performance required to make and break flange connections correctly
- Identify the tasks
- Inspect the job site
- Confirm whether isolations are completed as per the standard
- Confirm hazard controls
- Coordinate with relevant personnel
- Select suitable tools
- Check the calibration and certifications of tools
- Complete checklists and other required documentation
- Plan and prepare for job
- Break flange in accordance with flange management procedure
- Inspect flange and components
- Make flange joint in accordance with flange management procedure
- Finish the job.
- Case studies, Troubleshooting and problem solving
Procedures and standards of Break Flanges
- Prepare tools with care and accuracy
- Connect with required drain lines
- Undo nuts as per standard procedures
- Split flange and drain the pipe
- Identify any skills escalations
- Management of open pipes
- Complete checklists and other required documentation
Inspect flange and components
- Inspect removed gasket for indications of flange problems
- Assess cold pull and refer to appropriate personnel if required
- Assess degree of misalignment and refer to appropriate personnel if required
- Clean and inspect flange surface both front and back
- Check studs and nuts
- Confirm compliance of components and refer to appropriate personnel as required
- Identify any problems and take action.
Procedures and standards of Make Flange Joint
- Select the appropriate gasket
- Check whether all components are as per the specifications
- Apply lubrication as required
- Complete the initial assembly of the unit
- Insert the blind as required
- Attach the drain as required
- Re-check the gasket
- Re-check the alignments of the components
- Tighten components using the relevant tools
- Use torque calibration charts
- Complete checklists and other required documentation.
Finish the job
- Make a final check of joint alignment
- Organize required checks
- Confirm joint integrity as required
- Complete checklists and records as required
The important of safe isolation of plant and equipment techniques.
- Safe isolation steps
- 12 step isolation procedure
- Types of isolation in safety
- Isolation procedure in workplace
- Positive isolation
- Symptoms of absence of safe isolation of plant and equipment techniques (cases Study).
PTW work permit introduction
PURPOSE
- 1-PROTECT PERSON
- 2-PROTECT EQUIPMENT
- 3-PROTECT OTHERS
- 4-PROTECT ENVIRONOMENT
Objectives
- 1-CONTROL THE JOB
- 2-DETERMINE ATHORIZATION
- 3-NOT TO DUPLICATE THE WORK
- 4-TO MAKE RECORDS
Flanges Maintenance Management
- Inspection & testing.
- Causes of corrosion and failures in flanges.
- Preventative maintenance bolting.
- Preventative maintenance bolting procedure.
- Flange system records.
- Understand care of flanges and gaskets.
The impact of incorrect fitting of pipe and flanges and the main reasons for incorrect fitting.
- The main issues for flange leak in details
- What are the benefits of the Immediate Leak Detection?
- Impact of incorrect fitting.
Serious Incidents During Flange Bolting and Unbolting
- Safety Precautions
- Study of incidents.