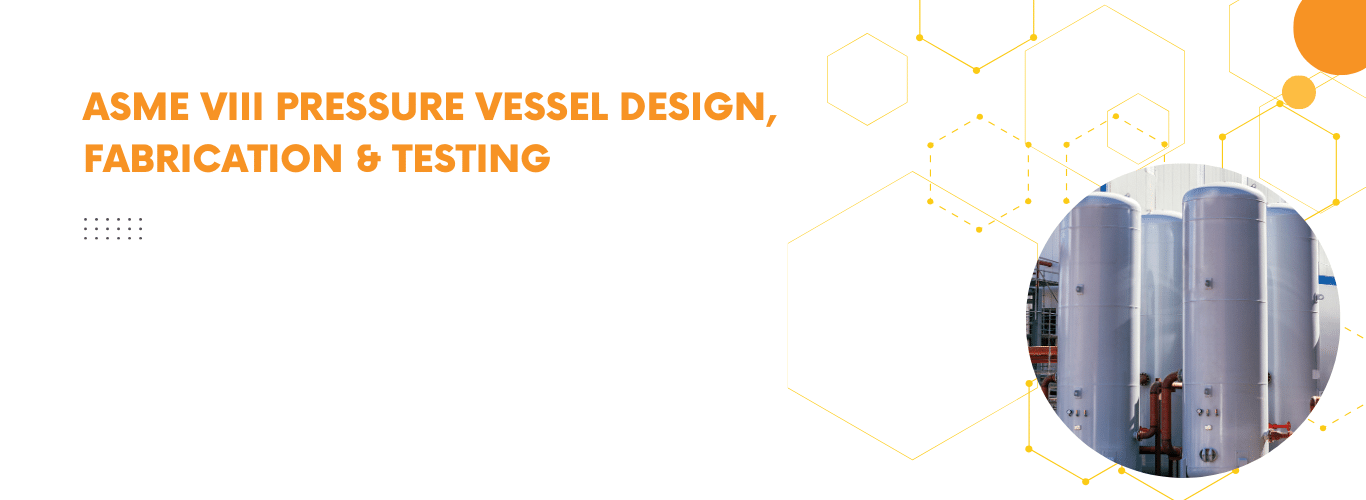
Course Description
The course is designed to provide delegates with a detailed and up-to-date overview of ASME VIII pressure vessel design, fabrication and testing. The course will help the participants to use the fabrication rules for various materials and fabrication methods including forging, casting and welding and distinguish material properties and requirements for low temperature and high temperature applications.
Participants will determine how pressure vessels are fabricated, mainly with regard to welding. Further, they will be able to employ the post weld heat treatment requirements of UCS 56 and practice the concept of temper bead welding as an in-service alternative to post weld heat treatment.
The course will further discuss the concept of the “The ASME Stamp”, where the national board fits into the ASME Scheme and where other standards such as API 510 are used. Participants will gain knowledge on the non-destructive methods and will be able to implement the proper procedures of hydrostatic and pneumatic tests and distinguish what it is designed to achieve. The course also covers the proper management of pressure vessel nameplates, stamping, documentation requirements, manufacturer’s data report and data book compilation.
Course Objectives
Upon the successful completion of this course, each participant will be able to:
- Apply the design rules of ASME VIII including rules governing shell thickness, head thickness, nozzles loadings, MAWP and NDT/NDE
- Use the fabrication rules for various materials and fabrication methods including forging, casting and welding
- Distinguish material properties and requirements for low temperature and high temperature applications
- Determine how pressure vessels are fabricated, mainly with regard to welding
- Employ the post weld heat treatment requirements of UCS 56 and practice the concept of Temper Bead Welding as an in-service alternative to post weld heat treatment
- Identify the concept of “The ASME Stamp” and discuss how to become an accredited fabricator; what it means to the Fabricator and what it means to the Purchaser
- Discuss where the National Board fits into the ASME Scheme and where other standards such as API 510 are used
- Gain an in-depth knowledge on the Non-Destructive Testing methods, what each method can detect and what it cannot detect and how to apply “Acceptance Criteria” from various Codes
- Implement the proper procedures of Hydrostatic and Pneumatic tests and distinguish what it is designed to achieve
- Manage Pressure Vessel nameplates, stamping, documentation requirements, Manufacturer’s Data Report and Data Book compilation
Who Should Attend
Those who are involved in the design, fabrication and testing of pressure vessels and for engineers who want to know more or move to this very interesting engineering area. Further, engineers involved in maintenance, repair and flaw evaluation of pressure vessels will also have a need for this course.
Delivery Method:
The course will be delivered through a combination of lectures, case studies, group discussions, and practical exercises. Participants will engage in interactive sessions to enhance learning and practical application of concepts.
Course Outlines:
Day-1
- Introduction to the ASME Boiler & Pressure Vessel Code
- Introduction to Section VIII, Division 1
- General & Material Requirements
- Design for Internal Pressure & External Pressure
- Vessels under Internal Pressure – Shell and Head Calculations
- UG-27 Thickness of Shells under Internal Pressure
- Vessels under Internal Pressure – Shell and Head Calculations.
Day-2
- Design of Formed Heads UG-32 Formulas and Rules for Using Formed Heads
- Design of Openings
- Introduction to Materials & the requirements
- Service Restrictions – Joint Efficiencies – Radiography
- UW-3 Weld Categories
- UW-51 RT Examination of Welded Joints
- UW-52 Spot Examination of Welded Joints.
Day-3
- Materials for Low Temperature Service
- Brittle Fracture Considerations
- Material Toughness Requirements & Charpy Impact Testing
- Materials for High Temperature Service
- Creep Testing.
Day-4
- Fabrication :Material Identification
- Material Certification
- Introduction to Welding & Basic Welding Processes
- Welding Procedures–The WPS & the PQR & Welder Qualifications
- Welding Variables–What Are Essential, Non-Essential & Supplementary Variables?
- Post Weld Heat Treatment.
Day-5
- NDE Requirements
- Methods Used • Advantages & Limitations of Each
- Hydrostatic & Pneumatic Testing According to ASME Sec. VIII Div.1
- Data Report & Stamping
- Example Problems & Discussion.